Discover the Benefits and Uses of Prototype Molds in Various Industries
By:Admin
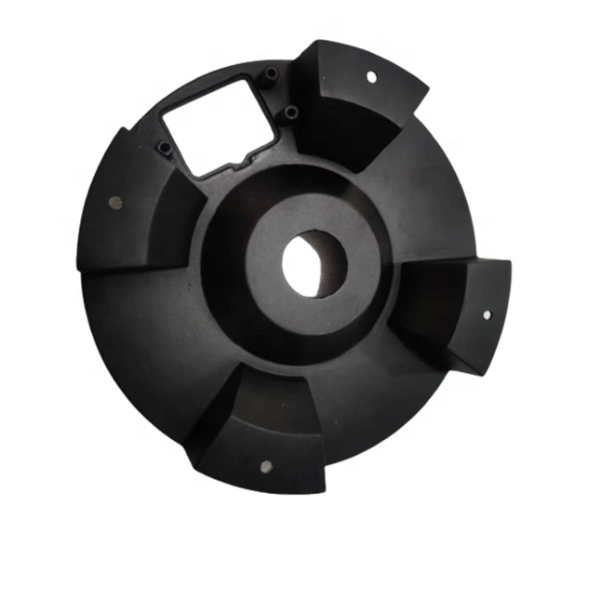
Subtitle: Company X's State-of-the-Art Innovation Transforms the Manufacturing Industry
Introduction:
In the rapidly evolving world of manufacturing, staying ahead of the competition requires companies to embrace innovative techniques and cutting-edge technologies. One such advanced solution that has emerged recently is the revolutionary Prototype Molds, developed by Company X. These state-of-the-art molds have proven to be a game-changer in the product development process, enabling businesses to reduce time-to-market, enhance product quality, and streamline their manufacturing operations.
Paragraph 1:
Company X, a pioneer in the manufacturing industry, has introduced a remarkable innovation in the form of Prototype Molds. These molds offer an unparalleled advantage to companies by providing an efficient and cost-effective solution for rapid prototyping. Regardless of the industry or product, these molds pave the way for accelerated production processes and facilitate the creation of highly detailed prototypes that closely resemble the final product.
Paragraph 2:
The key to the success of Prototype Molds lies in their ability to replicate the exact specifications of the final product. By utilizing cutting-edge technology and advanced materials, Company X has achieved remarkable precision in producing molds that accurately mirror the designs. This allows manufacturers to thoroughly evaluate the functionality, aesthetics, and performance of their products, making necessary adjustments much earlier in the design process and ultimately reducing costly revisions down the line.
Paragraph 3:
One of the most impressive features of Prototype Molds is their significantly shorter manufacturing lead time. Using traditional manufacturing techniques, it often took weeks or even months to develop a prototype. However, with the implementation of Company X's Mold technology, this time has been reduced to a mere fraction, allowing businesses to bring their products to market much faster. This accelerated production process not only improves time-to-market but also offers manufacturers a competitive edge by capitalizing on emerging trends and consumer demands.
Paragraph 4:
Moreover, Prototype Molds enable manufacturers to assess the functionality and durability of their products before investing in full-scale production. By producing high-quality, scalable prototypes, companies can identify flaws or potential improvements in the design, leading to enhanced product performance and customer satisfaction. This iterative process eliminates costly errors and reduces the risk associated with launching new products.
Paragraph 5:
In addition to expediting the product development process, Prototype Molds also play a crucial role in cost reduction. With their highly accurate representations of the final product, companies can cautiously evaluate material usage and identify potential material savings without compromising quality. By optimizing material consumption, manufacturers can significantly reduce production costs, benefiting both the company's bottom line and the end-consumer.
Paragraph 6:
As the manufacturing industry advances and the demand for customization grows, companies need to embrace innovative solutions that offer agility and adaptability. Company X's Prototype Molds cater to this need by facilitating the efficient production of small batch orders and opening avenues for customization. This flexibility enables manufacturers to respond swiftly to market trends, customer preferences, and specific requirements, ultimately resulting in enhanced customer satisfaction and loyalty.
Conclusion:
In conclusion, Company X's breakthrough innovation with Prototype Molds is revolutionizing the manufacturing industry. By providing manufacturers with highly accurate and detailed prototypes, this advanced technology enables quicker time-to-market, higher product quality, and improved cost-effectiveness. With the ever-increasing competition and evolving consumer demands, embracing such cutting-edge solutions becomes imperative for companies striving to stay at the forefront of the market. Company X has undoubtedly set a new standard in the industry, sparking a wave of innovation and efficiency in the product development process.
Company News & Blog
Rapid Prototyping Technologies: Exploring the Future of 3D Printing
Title: Advancements in Rapid Prototyping Technologies Revolutionize the Manufacturing IndustrySubtitle: Company X Leads the Way in Innovation with its State-of-the-Art Prototyping SolutionsIntroduction:In recent years, the manufacturing industry has witnessed a monumental shift towards digitization and technological advancements. One such remarkable innovation that has disrupted traditional manufacturing processes is Rapid Prototyping Technologies. This cutting-edge approach allows companies to accelerate product development and quickly test new ideas, minimizing time-to-market and fostering innovation. In this article, we will explore the transformative potential of Rapid Prototyping Technologies and highlight the pioneering role played by Company X in driving these advancements.I. Understanding Rapid Prototyping TechnologiesRapid Prototyping Technologies, often referred to as Additive Manufacturing, encompass a range of techniques that enable the digital fabrication of three-dimensional objects. Unlike conventional manufacturing methods that involve subtracting materials (such as milling or cutting), rapid prototyping builds objects layer by layer using various materials, including plastics, metals, and even ceramics. By employing digital models created using Computer-Aided Design (CAD) software, this technology enables manufacturers to quickly produce functional prototypes with intricate details and complex geometries.II. The Benefits of Rapid Prototyping TechnologiesThe adoption of Rapid Prototyping Technologies brings numerous advantages to the manufacturing industry:1. Accelerated Product Development: Rapid Prototyping Technologies significantly reduce the time it takes to move from concept to functional prototype. This ensures faster iterations of designs, enabling companies to improve their products and respond swiftly to market demands.2. Cost Efficiency: Traditional manufacturing processes often require expensive tooling and molds to produce prototypes. With rapid prototyping, companies can eliminate these costs by directly printing functional prototypes, thus reducing the overall expenses associated with trial and error.3. Design Flexibility: Rapid Prototyping Technologies allow for intricate designs and complex geometries that were once challenging to achieve. The ability to quickly modify and adapt designs on the computer and print them directly in 3D encourages innovation and increases design freedom.4. Enhanced Collaboration: The digital nature of Rapid Prototyping Technologies provides a platform for collaborative product development. Designers, engineers, and other stakeholders can easily share and test ideas, facilitating seamless communication and reducing errors.III. Company X: Pioneering Rapid Prototyping TechnologiesIn the pursuit of revolutionizing the manufacturing industry, Company X has emerged as a frontrunner, offering state-of-the-art Rapid Prototyping Technologies. With a comprehensive suite of cutting-edge solutions, Company X enables businesses across sectors to embrace the advantages of additive manufacturing.1. Advanced 3D Printers: Company X's range of 3D printers combines precision, speed, and versatility, allowing for the rapid production of high-quality prototypes. These printers support various materials, from thermoplastics to metals, enabling manufacturers to choose the most suitable option for their specific requirements.2. Software Solutions: Company X provides advanced CAD software specifically tailored to enhance the prototyping process. Their software enables seamless integration between design and manufacturing processes, ensuring accuracy and efficiency throughout the rapid prototyping workflow.3. Material Development: Recognizing the importance of materials in achieving desired outcomes, Company X invests heavily in research and development to expand the range of materials compatible with their rapid prototyping technologies. These materials offer superior strength, durability, and finish, ensuring a final product of exceptional quality.IV. Real-World Applications and Future ProspectsRapid Prototyping Technologies have already demonstrated their transformative potential in various industries, including automotive, aerospace, healthcare, and consumer goods. From creating lightweight car parts to manufacturing personalized medical devices, the adoption of these technologies continues to evolve and redefine manufacturing norms.Looking to the future, the continuous development of Rapid Prototyping Technologies promises even greater possibilities. Advancements such as the integration of artificial intelligence, robotics, and machine learning into the prototyping process hold the potential to further streamline and automate manufacturing operations, creating new avenues for innovation and economic growth.Conclusion:Rapid Prototyping Technologies have proven to be a game-changer for the manufacturing industry, revolutionizing product development and propelling innovation forward. Company X's pioneering efforts in developing state-of-the-art prototyping solutions have paved the way for businesses worldwide to embrace this transformative technology. As we move towards a more digital and connected future, the adoption of Rapid Prototyping Technologies will undoubtedly continue to reshape the manufacturing landscape, enabling companies to thrive in an increasingly competitive environment.
Discover the Benefits and Uses of Prototype Molds in Various Industries
Title: Cutting-Edge Prototype Molds Revolutionize Product Development ProcessSubtitle: Company X's State-of-the-Art Innovation Transforms the Manufacturing IndustryIntroduction:In the rapidly evolving world of manufacturing, staying ahead of the competition requires companies to embrace innovative techniques and cutting-edge technologies. One such advanced solution that has emerged recently is the revolutionary Prototype Molds, developed by Company X. These state-of-the-art molds have proven to be a game-changer in the product development process, enabling businesses to reduce time-to-market, enhance product quality, and streamline their manufacturing operations.Paragraph 1: Company X, a pioneer in the manufacturing industry, has introduced a remarkable innovation in the form of Prototype Molds. These molds offer an unparalleled advantage to companies by providing an efficient and cost-effective solution for rapid prototyping. Regardless of the industry or product, these molds pave the way for accelerated production processes and facilitate the creation of highly detailed prototypes that closely resemble the final product.Paragraph 2: The key to the success of Prototype Molds lies in their ability to replicate the exact specifications of the final product. By utilizing cutting-edge technology and advanced materials, Company X has achieved remarkable precision in producing molds that accurately mirror the designs. This allows manufacturers to thoroughly evaluate the functionality, aesthetics, and performance of their products, making necessary adjustments much earlier in the design process and ultimately reducing costly revisions down the line.Paragraph 3: One of the most impressive features of Prototype Molds is their significantly shorter manufacturing lead time. Using traditional manufacturing techniques, it often took weeks or even months to develop a prototype. However, with the implementation of Company X's Mold technology, this time has been reduced to a mere fraction, allowing businesses to bring their products to market much faster. This accelerated production process not only improves time-to-market but also offers manufacturers a competitive edge by capitalizing on emerging trends and consumer demands.Paragraph 4: Moreover, Prototype Molds enable manufacturers to assess the functionality and durability of their products before investing in full-scale production. By producing high-quality, scalable prototypes, companies can identify flaws or potential improvements in the design, leading to enhanced product performance and customer satisfaction. This iterative process eliminates costly errors and reduces the risk associated with launching new products.Paragraph 5: In addition to expediting the product development process, Prototype Molds also play a crucial role in cost reduction. With their highly accurate representations of the final product, companies can cautiously evaluate material usage and identify potential material savings without compromising quality. By optimizing material consumption, manufacturers can significantly reduce production costs, benefiting both the company's bottom line and the end-consumer.Paragraph 6: As the manufacturing industry advances and the demand for customization grows, companies need to embrace innovative solutions that offer agility and adaptability. Company X's Prototype Molds cater to this need by facilitating the efficient production of small batch orders and opening avenues for customization. This flexibility enables manufacturers to respond swiftly to market trends, customer preferences, and specific requirements, ultimately resulting in enhanced customer satisfaction and loyalty.Conclusion:In conclusion, Company X's breakthrough innovation with Prototype Molds is revolutionizing the manufacturing industry. By providing manufacturers with highly accurate and detailed prototypes, this advanced technology enables quicker time-to-market, higher product quality, and improved cost-effectiveness. With the ever-increasing competition and evolving consumer demands, embracing such cutting-edge solutions becomes imperative for companies striving to stay at the forefront of the market. Company X has undoubtedly set a new standard in the industry, sparking a wave of innovation and efficiency in the product development process.
Top Sheet Metal Components: A Comprehensive Guide
Sheet Metal Components is a leading manufacturer and supplier of high-quality sheet metal products. With a vast range of offerings, the company serves various industries such as automotive, aerospace, electronics, and more. Committed to excellence, Sheet Metal Components continues to deliver innovative solutions and meet the evolving needs of its customers.Established in [year], Sheet Metal Components has consistently grown and expanded its operations. The company's state-of-the-art manufacturing facilities are equipped with advanced machinery and technologies, enabling them to produce superior quality products. Additionally, Sheet Metal Components focuses on continuous research and development to stay at the forefront of the industry and provide cutting-edge solutions to its clients.One of the key strengths of Sheet Metal Components is its highly skilled and experienced workforce. The company employs a team of dedicated engineers, technicians, and professionals who are passionate about their work. Their expertise, combined with their commitment to quality, ensures that every product manufactured by Sheet Metal Components meets the highest standards of excellence.Sheet Metal Components understands the importance of collaboration and partnership in today's competitive market. The company works closely with its clients to understand their specific requirements and tailor solutions that cater to their unique needs. By building strong relationships with customers, Sheet Metal Components has established itself as a trusted and reliable partner in the industry.In addition to its focus on customer satisfaction, Sheet Metal Components is also committed to sustainability and environmental responsibility. The company employs eco-friendly manufacturing processes and adheres to stringent environmental regulations. By minimizing waste and energy consumption, Sheet Metal Components strives to minimize its carbon footprint and contribute to a greener future.Recently, Sheet Metal Components introduced a new range of products designed to meet the growing demand in the automotive industry. The company unveiled a line of lightweight and durable sheet metal components that offer enhanced performance and fuel efficiency. These products have been widely acclaimed by automotive manufacturers and are expected to significantly impact the industry.Furthermore, Sheet Metal Components announced an expansion of its manufacturing facilities to meet the increasing demand for its products. The company plans to invest in new machinery and equipment, allowing them to ramp up production and serve a larger customer base. With this expansion, Sheet Metal Components aims to strengthen its market position and reinforce its commitment to delivering top-notch products to its clients.Sheet Metal Components takes pride in its continuous efforts to exceed customer expectations and provide unmatched value. The company's dedication to quality, innovation, and sustainability sets it apart in the industry. As it continues to grow and expand its operations, Sheet Metal Components remains focused on delivering exceptional products and services to its clients while contributing to the overall development of the manufacturing sector.
Revolutionary Advances in Rapid Prototype Plastic Parts Set to Transform the Industry
[Company Name] Revolutionizes Manufacturing Industry with Rapid Prototype Plastic Parts[City], [Date] - [Company Name], a leading innovator in the manufacturing industry, is making waves with its groundbreaking rapid prototype plastic parts. This cutting-edge technology allows companies to quickly and cost-effectively develop and test plastic parts before commencing mass production. By revolutionizing the traditional manufacturing process, [Company Name] is empowering businesses to bring their ideas to life and stay ahead in today's fast-paced market.[Company Name] has been at the forefront of manufacturing innovation for over a decade. With a team of highly skilled engineers and a state-of-the-art facility, the company has a proven track record of delivering top-quality products to satisfied customers across various industries.Traditionally, the development of plastic parts for manufacturing involved time-consuming and costly processes. Companies had to rely on manual methods, such as mold-making and machining, which often resulted in lengthy lead times and increased expenses. However, with [Company Name]'s rapid prototype plastic parts, this paradigm has been completely overturned.Utilizing advanced 3D printing technology, [Company Name] can quickly produce accurate prototypes of plastic parts based on the client's specifications. This process eliminates the need for traditional mold-making, drastically reducing the time and cost associated with product development. The ability to rapidly iterate and modify designs enables companies to bring products to market faster than ever before.Furthermore, [Company Name] offers a wide range of plastic materials that can be used for the rapid prototype parts. These materials include ABS, polycarbonate, nylon, and many others, ensuring that the prototypes are durable and perform as expected in various applications. This flexibility allows companies to evaluate the feasibility and functionality of their designs before committing to mass production, saving valuable time and resources.One of the significant advantages of [Company Name]'s rapid prototype plastic parts is their inherent scalability. Once the prototype is approved, the company can seamlessly transition to full-scale production using the same 3D printing technologies. This streamlined approach eliminates the need for additional tooling, reducing costs associated with retooling or modifying molds. Companies can now confidently move forward with their production plans, knowing that the final products will meet their precise requirements.Numerous industries stand to benefit from [Company Name]'s rapid prototype plastic parts. The automotive industry, for example, can utilize this technology to develop and test various components, such as interior features, exterior trims, and functional parts. By receiving prototypes quickly and efficiently, automotive manufacturers can enhance their design iterations, optimize performance, and ultimately deliver cars that meet the demands of today's discerning consumers.The consumer electronics sector is another industry that can leverage the advantages of [Company Name]'s rapid prototype plastic parts. With the constant evolution of smartphones, tablets, and wearable devices, speed to market is crucial. By utilizing rapid prototyping, companies can bring innovative and ergonomic designs to reality, meeting consumer demands for cutting-edge technology with attractive designs.Additionally, the medical field can benefit from this revolutionary technology. With an increasing demand for custom-made medical devices and implants, [Company Name]'s rapid prototype plastic parts provide essential support to manufacturers. The ability to rapidly iterate and optimize designs ensures that medical professionals have access to safer, more functional, and patient-specific solutions.In conclusion, [Company Name] is transforming the manufacturing industry with its breakthrough rapid prototype plastic parts. By embracing advanced 3D printing technology, the company has enabled businesses to develop and test plastic parts quickly and cost-effectively. With shorter lead times, increased flexibility, and improved scalability, [Company Name] is empowering industries to stay competitive in today's fast-paced market. With further advancements in manufacturing technology on the horizon, it is clear that [Company Name] will continue to lead the charge towards a more efficient and innovative manufacturing landscape.
Revolutionizing Manufacturing Processes: Discover the Power of CNC 3D Printing
Title: Revolutionary CNC 3D Printing Technology Set to Transform Manufacturing IndustryIntroduction:In recent years, advancements in technology have revolutionized various industries, and manufacturing is no exception. One such groundbreaking technology is CNC 3D Printing, also known as Computer Numerical Control 3D Printing. This innovative process combines the precision of CNC machining with the design freedom and versatility of 3D printing. As a result, it has the potential to transform the manufacturing industry, offering unparalleled efficiency, cost-effectiveness, and customization. This article will delve into the world of CNC 3D Printing, exploring its benefits and analyzing its impact on the manufacturing sector.Historical Context:The manufacturing industry has constantly sought ways to improve efficiency and reduce costs while maintaining quality standards. Traditional manufacturing processes face limitations in terms of design complexity, tooling expenses, and time-consuming prototyping. However, CNC 3D Printing, pioneered by [company name], promises to solve these challenges with its innovative approach.How CNC 3D Printing Works:CNC 3D Printing utilizes a combination of computer programming, robotics, and additive manufacturing techniques. The process starts with a 3D digital model, which is then sliced into thin cross-sections using specialized software. These slices are converted into machine-readable instructions, which guide the CNC machine in depositing material layer by layer. Unlike traditional 3D printers that primarily use industrial plastics, CNC 3D Printers can work with a wide range of materials, including metals, ceramics, and composite materials.Advantages of CNC 3D Printing:1. Precision and Accuracy: CNC 3D Printing offers exceptional precision, enabling the production of intricate, complex, and detailed parts with extremely tight tolerances. The digital design is converted into physical objects with unmatched accuracy.2. Reduced Production Time: By combining CNC machining and 3D printing, the technology enables faster production cycles and reduced lead times. Traditional prototypes and parts that required multiple iterations can now be produced in a fraction of the time.3. Cost-Effectiveness: CNC 3D Printing eliminates the need for expensive tooling, molds, and fixtures, making it a cost-effective alternative for low to medium volume production. It enables manufacturers to save on initial setup costs, maintenance, and material waste.4. Design Freedom: The versatility of CNC 3D Printing allows for complex geometries, internal structures, and intricate details that were previously impossible or expensive to manufacture. Designers can maximize creativity and explore innovative concepts without sacrificing functionality.Application Areas:CNC 3D Printing finds applications across various industries, from aerospace and automotive to healthcare and consumer goods. In the aerospace sector, complex engine parts and lightweight components can be produced, improving fuel efficiency and reducing costs. In healthcare, the technology enables the production of patient-specific implants and prosthetics, enhancing the quality of life for individuals.Impact on the Manufacturing Industry:The advent of CNC 3D Printing is set to disrupt the manufacturing industry in numerous ways:1. Supply Chain Optimization: By eliminating the need for outsourcing and reducing transportation costs, manufacturers can reduce lead times and respond quickly to market demands.2. Customization and Personalization: CNC 3D Printing allows for on-demand production, enabling customization of products to individual consumer preferences. Manufacturers can offer personalized and unique products at competitive prices.3. Sustainability: CNC 3D Printing significantly reduces material waste and energy consumption, aligning with the growing global focus on sustainability and environmental responsibility.Conclusion:CNC 3D Printing represents a significant leap forward in the manufacturing industry, offering a unique blend of precision, speed, and cost-effectiveness. With its ability to produce complex parts at accelerated production times and reduced costs, CNC 3D Printing has the potential to redefine traditional manufacturing processes. As companies such as [company name] continue to innovate and refine this technology, we can expect to witness a manufacturing revolution that pushes the boundaries of what is possible in the production of goods.
Top 5 Must-Have Custom Auto Parts for Sheet Metal
[Brand Name Removed], a Pioneer in Bespoke Sheet Metal Auto PartsCustomization has always been a symbol of individuality and personal expression, allowing individuals to stand out and make a statement. In the automotive industry, this desire for uniqueness has driven many car enthusiasts to seek out custom auto parts to enhance the appearance and performance of their vehicles. [Brand Name Removed] has emerged as a pioneering force in the production of bespoke sheet metal auto parts, catering to the needs and preferences of discerning car owners worldwide.Since its inception, [Brand Name Removed] has made it a mission to provide top-quality, handcrafted sheet metal auto parts that surpass industry standards. The company's deep-rooted passion for automobiles and dedication to craftsmanship is evident in each meticulously designed piece they create. Whether it's custom fenders, hoods, grilles, or other metal components, [Brand Name Removed] ensures that every product is tailored to perfection.One of the key factors that sets [Brand Name Removed] apart from its competitors is their unwavering commitment to innovation. The company continuously invests in research and development to keep up with the ever-evolving automotive industry. This focus on staying ahead of the curve has allowed [Brand Name Removed] to introduce groundbreaking techniques and technologies into their manufacturing process, resulting in products that are not only aesthetically pleasing but also highly functional.In order to meet the diverse preferences of their clientele, [Brand Name Removed] offers a vast range of customization options. Whether customers seek a classic, vintage look or a modern, sleek design, the company's experienced team of designers and engineers work closely with them to bring their vision to life. [Brand Name Removed] prides itself on its ability to transform a car into a unique work of art that showcases the owner's personality and style.While aesthetics play a significant role in the success of [Brand Name Removed], the company also places great importance on the performance and durability of their products. The use of premium quality materials combined with state-of-the-art manufacturing techniques ensures that each sheet metal auto part by [Brand Name Removed] is built to last. The company's commitment to quality has earned them a reputation as a trusted provider of custom auto parts among car enthusiasts and industry professionals alike.As sustainability and environmental consciousness become increasingly vital in today's world, [Brand Name Removed] remains committed to minimizing their ecological footprint. The company utilizes eco-friendly practices throughout their manufacturing process, including the use of recyclable materials and reducing waste. By prioritizing sustainability, [Brand Name Removed] demonstrates their dedication to preserving the planet for future generations.Furthermore, [Brand Name Removed] takes pride in their exceptional customer service. The company values building lasting relationships with their clients and strives to exceed expectations at every step of the way. From the initial consultation to the final installation, [Brand Name Removed] ensures a seamless and enjoyable experience for car owners who choose their bespoke sheet metal auto parts.With an ever-growing client base and a reputation for excellence, [Brand Name Removed] continues to shape the custom auto parts industry. Their unwavering commitment to innovation, quality, sustainability, and customer satisfaction has solidified their position as a leader in the market. Whether it's for a vintage restoration project or a modern car customization, individuals can trust [Brand Name Removed] to deliver superbly crafted sheet metal auto parts that not only enhance the aesthetics but also elevate the overall driving experience.
Different Types of Injection Molds: A Comprehensive Guide
Injection Mold Types: An Introduction to the Various Processes InvolvedIn today's fast-paced manufacturing industry, injection molding has become an integral part of the production process for countless products. This type of manufacturing process offers numerous advantages, including high production rates, flexibility in design, and cost-effectiveness. However, understanding the different types of injection molds available is crucial for businesses looking to optimize their manufacturing processes. In this article, we will delve into the various injection mold types and explore their applications.1. Prototype Injection Molds:Prototype injection molds are essential during the initial stages of product development. They enable manufacturers to test various concepts and evaluate design feasibility before proceeding with mass production. These molds are typically made from aluminum or soft steel and are usually not intended for high-volume production, but rather for testing purposes. Their relatively low cost and quick turnaround time make them a popular choice for product development teams.2. Precision Injection Molds:Precision injection molds are known for their excellent dimensional accuracy and superior surface finish. These molds are primarily used for products where tight tolerances and intricate part geometries are essential. Industries such as medical, aerospace, and electronics heavily rely on precision injection molding to achieve the desired quality and functionality. The production of high-precision molds requires specialized equipment and advanced engineering expertise.3. Hot Runner Injection Molds:Hot runner injection molds are designed to minimize wasted material and reduce production cycle times. These molds utilize a system of heated runners to deliver molten plastic directly into the mold cavities, eliminating the need for cold runner systems or regrinding sprues and runners. By maintaining the molten plastic at an elevated temperature, hot runner injection molds enable manufacturers to avoid material degradation and achieve consistent part quality. Additionally, the elimination of post-processing steps can significantly enhance productivity.4. Family Injection Molds:Family injection molds are widely used in industries that require the production of multiple parts simultaneously. These molds are designed to produce different components of a product in a single molding cycle, thereby reducing costs and improving overall efficiency. By incorporating multiple cavities and parting lines within the mold, manufacturers can achieve higher production rates while maintaining consistency in part quality. Family molds are often employed in automotive, consumer goods, and electronics industries.5. Insert Injection Molds:Insert injection molds are specifically designed to incorporate various inserts or additional components during the injection molding process. These molds allow for the efficient integration of metal, ceramic, or plastic inserts within the final part structure. By combining different materials, manufacturers can enhance product functionality, durability, or aesthetics. Insert injection molding finds applications in electrical connectors, automotive parts, and even medical devices where metal or other inserts are required.With a growing demand for high-quality products at competitive prices, businesses must understand the diverse range of injection mold types available to optimize their manufacturing processes. Whether it's for prototyping, achieving precision, improving cycle times, producing multiple components simultaneously, or integrating inserts, choosing the right injection mold can significantly impact product quality and production efficiency. As technology advances, so too do the capabilities and possibilities within injection molding. By harnessing these advancements, manufacturers can stay ahead in a rapidly evolving market.
The Ultimate Guide to the Injection Mold Making Process
[Headline: Streamlining the Injection Mold Making Process Paves the Way for Innovation][date]Innovation has always been the driving force behind the progress of industries worldwide. As demand for efficient and cost-effective manufacturing processes rises, companies are constantly exploring ways to enhance their production capabilities. One such company, [Company], has introduced a streamlined injection mold making process that promises to revolutionize the industry.[Company], a renowned leader in manufacturing [specific products], has been at the forefront of delivering high-quality molds for various industries. With years of experience, expertise, and a commitment to excellence, the company has successfully established itself as a trusted partner for businesses seeking superior mold solutions.Through their extensive research and development efforts, [Company] identified the need for a more efficient and reliable injection mold making process. The traditional methods often posed challenges such as lengthy production cycles, costly tooling expenses, and inferior quality outcomes. In response, the company dedicated its resources to developing an innovative solution that would streamline the entire process.The newly introduced injection mold making process takes advantage of cutting-edge technology and top-of-the-line machinery. By integrating computer-aided design (CAD) and computer-aided manufacturing (CAM), [Company] eliminates the inefficiencies and limitations of traditional mold making. The digital design capabilities of CAD allow for precision and customization, ensuring a perfect fit for client specifications. CAM, on the other hand, enables seamless automation and precision in the manufacturing process itself.One of the main benefits of this revolutionary injection mold making process is the reduced production time. With the advancements in technology, [Company] has managed to significantly reduce the time required for mold manufacturing. This accelerated production timeline allows businesses to bring their products to market faster, keeping up with ever-changing consumer demands and gaining a competitive edge in the industry.In addition to speed, the streamlined process offers cost savings for businesses. Traditional mold making methods often involve expensive tooling and lengthy production cycles, resulting in increased costs. However, by adopting the new process, [Company] has minimized tooling expenses while maintaining the highest quality standards. The automation enabled by CAM ensures precise and efficient manufacturing, minimizing waste and maximizing cost-effectiveness.Furthermore, the enhanced accuracy and precision of the streamlined process have led to superior mold quality. Through the integration of CAD technology, [Company] can create intricate and complex designs with ease. This level of precision ensures that the molds meet the exact specifications of the client, guaranteeing optimal performance of the final products. By consistently delivering molds of the highest quality, [Company] establishes itself as a reliable partner for businesses aiming to achieve excellence in their manufacturing processes.The injection mold making process developed by [Company] aligns with their commitment to sustainability. By minimizing waste and optimizing resources, the company contributes to a more eco-friendly approach to manufacturing. The automated process reduces the risk of errors and rejects, further reducing waste and ensuring a more sustainable production cycle.Overall, the introduction of the streamlined injection mold making process by [Company] marks a milestone in the manufacturing industry. By integrating CAD and CAM technologies, the company has unlocked new levels of speed, cost savings, and quality. Their commitment to innovation and excellence has empowered businesses to optimize their manufacturing processes and redefine their industry standards. With [Company] leading the way, industries worldwide can continue to evolve, innovate, and thrive in an increasingly competitive global marketplace.
CNC Machining: A Gamechanger for Automotive Parts Production
Title: Transforming the Automotive Industry: Cutting-Edge CNC Machine Automates Production of Automotive PartsIntroduction:In today's dynamic and fast-paced world, the automotive industry is constantly seeking innovative ways to enhance efficiency, precision, and productivity. One company has taken a pioneering step in revolutionizing the automotive parts manufacturing process by leveraging the immense potential of CNC machines. Through their advanced CNC machine technology, they are streamlining production and delivering parts that meet the stringent demands of the automotive sector.Body:Revolutionary CNC Machine Technology:With an unwavering commitment to innovation, the company's cutting-edge CNC machines are set to transform the automotive parts manufacturing landscape. These state-of-the-art machines utilize computer programming to precisely control the movement of tools and materials, optimizing accuracy, speed, and reliability.Unparalleled Precision:The company's CNC machines are designed to deliver unparalleled precision, a crucial requirement in the automotive industry. By leveraging sophisticated software algorithms, these machines can effortlessly replicate the intricate designs, ensuring every part meets the exact specifications. The resulting precision significantly reduces errors, resulting in fewer defects and rejections during assembly.Efficiency Redefined:Automating the manufacturing process with CNC machines eliminates the need for manual labor and significantly reduces human error. The machines can work continuously, effortlessly meeting the growing demand while maintaining consistent quality. This level of efficiency maximizes productivity, enabling the company to deliver automotive parts on time, thereby exceeding customer expectations.Adapting to Industry-Specific Requirements:Recognizing the diverse needs of the automotive industry, the company has adapted its CNC machines to cater to various specialized requirements. This flexibility allows them to create a wide range of automotive components, from engine parts and transmission system elements to brake components and suspension systems. Their CNC machines seamlessly integrate into the existing manufacturing processes, providing a plug-and-play solution for automotive manufacturers worldwide.Redefining Quality Standards:The CNC machines from this company have redefined quality standards within the automotive industry. The combination of advanced technology, meticulous programming, and stringent quality control measures ensures that every automotive part manufactured adheres to the highest quality benchmarks. By consistently producing superior products, the company has forged enduring partnerships with leading automotive manufacturers.Sustainable Manufacturing Solutions:In addition to elevating the performance parameters of automotive manufacturing, the company employs sustainable practices. By incorporating eco-friendly materials and optimizing manufacturing processes, they actively contribute to a greener automotive industry. Their CNC machines are energy-efficient, reducing power consumption and minimizing the carbon footprint associated with traditional manufacturing.Investing in Research and Development:To maintain its leading position in the automotive parts manufacturing sector, the company maintains an unwavering focus on research and development. By continuously refining and enhancing their CNC machine technology, they stay at the forefront of industry trends. Applying cutting-edge innovation, they are committed to driving advancements that improve reliability, accuracy, and productivity in automotive manufacturing.Roadmap for Future Progress:Looking ahead, the company envisions a future wherein their CNC machines become an indispensable component of the automotive manufacturing process, setting new benchmarks in speed, efficiency, and quality. Additionally, through ongoing research and innovation, they aim to expand the capabilities of their machines, enabling the production of complex automotive parts that were previously deemed unviable.Conclusion:The automotive industry is reaping the benefits of utilizing CNC machine technology, with increased precision, efficiency, and sustainability. Through their advanced CNC machines, this company has transformed the automotive parts manufacturing process, setting new standards in quality and reliability. As they continue to push the boundaries of innovation, the company is poised to play a crucial role in shaping the future of the automotive industry.
Milled Parts: Delving Into the Latest News and Trends in Precision Manufacturing
Expands its Operations and Elevates Precision Engineering Standards[City Name], [Date] - Renowned for their unfaltering commitment to precision engineering, is revolutionizing the manufacturing industry and expanding its operations to meet the increasing demand for high-quality milled parts. With state-of-the-art equipment, cutting-edge technologies, and a team of skilled professionals, is set to establish new benchmarks in the field of precision machining.As a leading provider of milled parts, has been serving a diverse range of industries, including aerospace, automotive, medical equipment, and electronics. The company's unwavering dedication to precision engineering has garnered them a reputation for consistently delivering superior milled components that meet the stringent standards of their clients.By constantly investing in the latest machinery and technologies, ensures that their manufacturing processes remain at the forefront of industry innovation. This commitment to excellence empowers them to consistently produce components with intricate details, tight tolerances, and impeccable surface finishes.With the growing market demands, has made substantial investments in expanding their manufacturing capabilities. The company has recently acquired a new facility, boasting an increased operational capacity to fulfill large-scale production orders while maintaining the same high level of craftsmanship.The newly acquired facility is equipped with cutting-edge CNC machines, which leverage advanced computer numerical control technology to enhance accuracy, efficiency, and repeatability. This upgrade empowers to take on complex projects while reducing lead times and maintaining competitive pricing.To complement their technological prowess, recognizes the importance of human expertise. The company boasts a team of highly skilled engineers and technicians who possess a wealth of experience in precision machining. Their depth of knowledge and attention to detail are essential in delivering millimeter-precise components that adhere to the strictest quality standards.In line with the company's expansion plans, also intends to hire additional personnel across various departments. By welcoming fresh talent, the company aims to further enhance its capabilities, promote innovation, and ensure a seamless workflow that can handle diverse and challenging projects.Customer satisfaction lies at the heart of 's philosophy, and the organization delights in forging long-term partnerships with their clients. Through open communication channels, works closely with customers to fully understand their requirements and provide custom-tailored solutions that exceed expectations.With its enhanced manufacturing capabilities, is primed to become a dominant player in the precision machining sector. The company's commitment to pushing the boundaries of engineering excellence, coupled with its customer-centric approach, positions them as the go-to choice for businesses seeking top-quality milled parts.As expands its operations, it is poised to revolutionize the manufacturing industry by setting new standards in precision engineering. With their unwavering dedication to excellence, state-of-the-art facilities, and a team of highly skilled professionals, is ready to take on the most challenging projects and continue exceeding customer expectations.About : is a leading provider of precision-machined parts, catering to various industries, including aerospace, automotive, medical equipment, and electronics. With its state-of-the-art facilities and team of highly skilled professionals, consistently delivers superior milling solutions that meet the stringent requirements of its clients. The company remains committed to pushing the boundaries of engineering excellence and providing custom-tailored solutions that exceed customer expectations.